Snackwatch
Emergency COVID containment
Immutouch is a product line I developed and deployed with my cofounders Joseph Toles and Justin Ith during the first weeks of the US COVID pandemic in March 2020. We entirely retooled our existing company, Slightly Robot, to do our part in flattening the curve.
Background
On March 1 2020, we received the first reports of a coronavirus-related death and human-to-human transmission just miles from our headquarters in Seattle. At the time, the CDC was imploring people not to wear masks, but to wash hands frequently and avoid touching facial mucous membranes where the virus could be introduced. Since people on average touch their faces around 23 times a day, this is no small ask. Having already developed detection and alert devices for hair pulling, skin picking, and nail biting with our Slightly Robot project, we felt it was our responsibility to apply that technology to the ballooning outbreak.
Development
Deploying Immutouch to the general public quickly enough to help flatten the curve required a tremendous feat of engineering. Although we had technology ready from Slightly Robot, we had to make several major changes to provide a quality and effective product. Both iOS and Android received a mobile update and we built, tested, and deployed a firmware patch that upsampled inertial measurements by a factor of 10 in order to better track the relatively quick face-touching gesture. We also built a new site, going live on all four in seven days.
Reception
Our new site went live on March 8 and instantly became a viral hit. The story was first picked up by geekwire and Techcrunch and from there spread to NBC, Forbes, CBS, and a lot of other places, getting as far as Vietnam. At the height of our hype, we were invited onto Fox Business News.
Deployment
Coping with demand was an immediate challenge. We exhausted our completed inventory within a day. We then set to work assembling the 400 or so incomplete inventory we had on hand with the help of friends, neighbors, and strangers on Craigslist. All available inventory was pre-sold by March 10 and we diverted all incoming orders to backorder. Assembling inventory from the parts on hand would take around two weeks, having converted our entire basement and living room into an assembly line and fulfillment center.
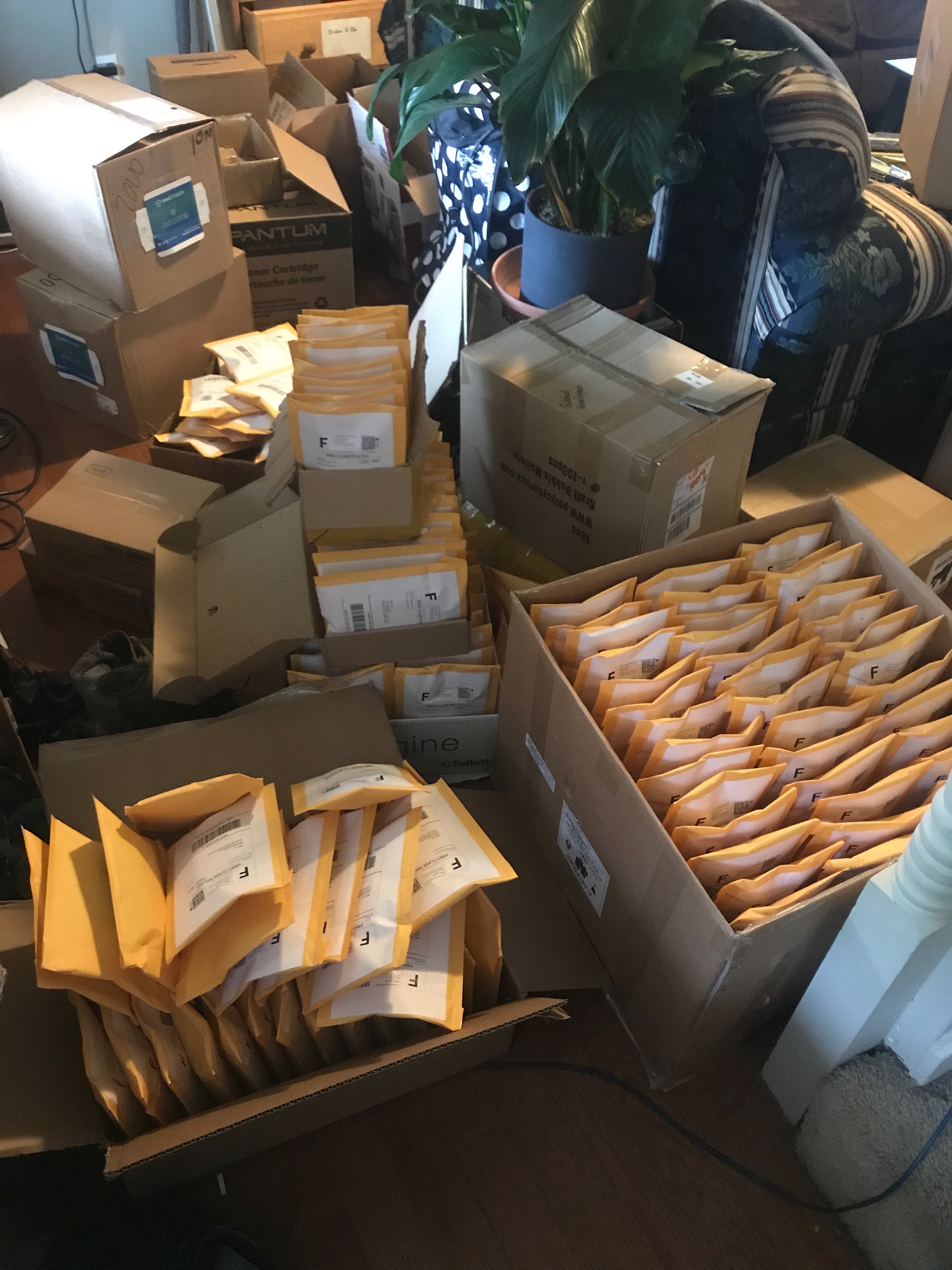
One days' worth of packages ready to ship.
At this point, we had around 1000 units on backorder, so I immediately began scaling production. We executed an entire PCB and housing redesign, prototype, and supply chain setup from scratch in two months. This was no easy task, in part because the pandemic had air cargo out of China at a standstill and fabricators across the States running on skeleton crews. Despite this all, we had new PCBs and arriving in April and housings arriving in May with product moving out the door the day after.
Ultimately we shipped thousands of units to the US and abroad. Feedback from users, especially medical professionals was extremely positive. Production continues to date.